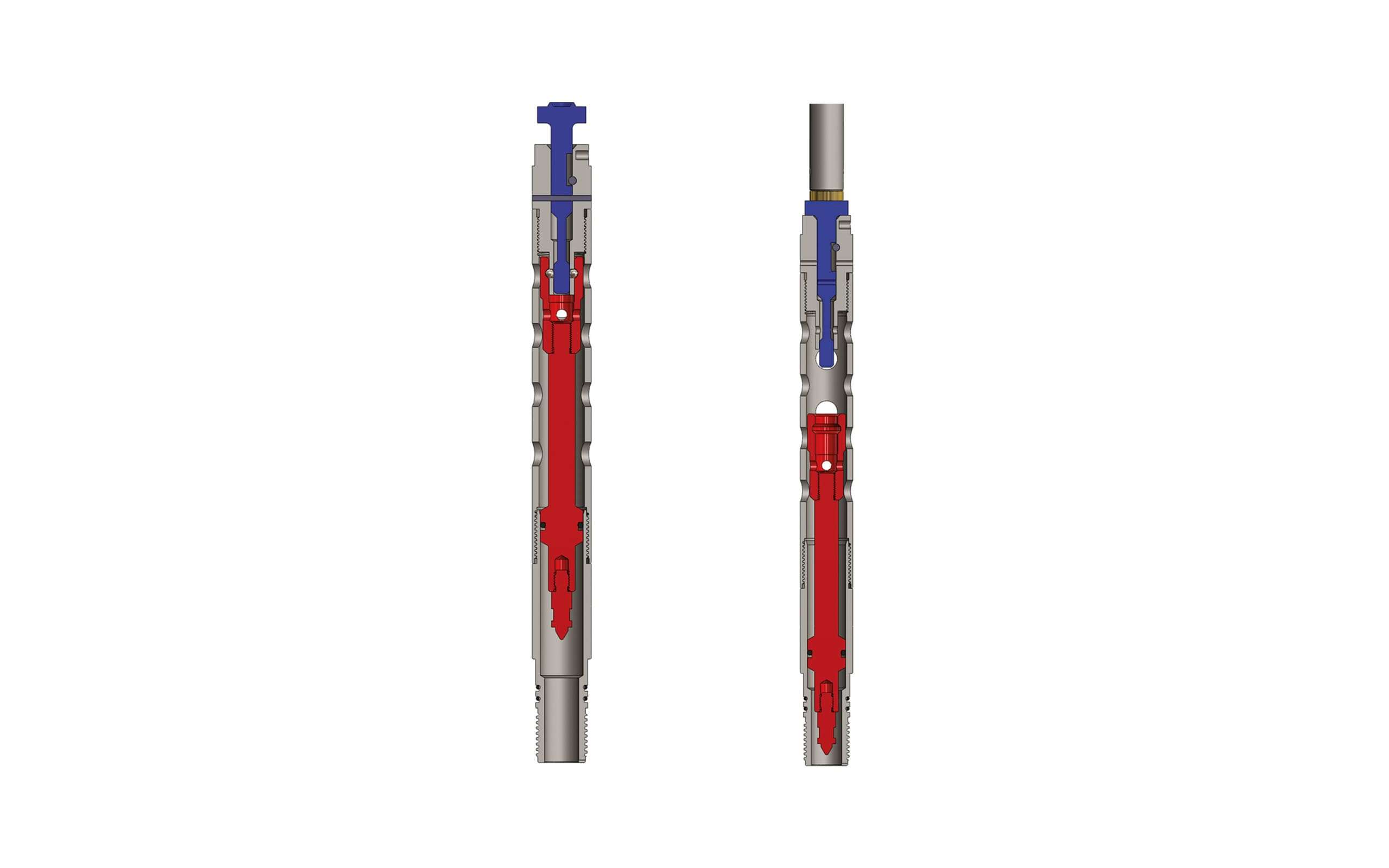
Drop Bar Hydrostatic Firing Heads
Drop Bar Hydrostatic Firing Heads can be operated at low hydrostatic pressure conditions, providing a high underbalanced environment when guns are fired.
Product summary
Drop Bar Hydrostatic Firing Heads can be operated at low hydrostatic pressure conditions, providing a high underbalanced environment when guns are fired.
The drop bar impacts a release rod and shears the retaining pin holding it in place which causes the rod to move down. This movement of the rod releases the firing piston. Hydrostatic pressure drives the firing piston down towards the percussion initiator. The firing pin located at the end of the firing piston strikes the percussion initiator which in turn detonates the gun assembly. As a safety feature, a minimum hydrostatic pressure is required on the firing piston when the drop bar impacts in order to operate.
The drop bar has a brass impression pad on the base of it which can be used to confirm impact with the release rod by identifying a familiar pattern on the impression. The upper end of the drop bar incorporates a standard slickline fishing neck.
There is also an option to utilize a direct impact firing head which does not require any hydrostatic pressure (no firing piston) to fire the gun assembly
Applications
TCP perforating
Underbalance and overbalance perforating
Straight wells with deviation less than 55°
Features
Designed to API RP-67 (Oilfield Explosive Safety) guidelines
Impression pad can confirm dop bar impact
High pressure version available
Firing head extensions offered upon requestRoller drop bars available for high deviation wells
Redress kits
Simple, reliable and rugged design
Benefits
Enhanced safety as cannot be detonated at surface or by electrical sources
Can be operated at low hydrostatic pressure conditions, providing a high underbalanced environment when guns are fired
Compatible with all Titan TCP firing systems
Extensions can reduce risk of debris settling on firing head
Cost effective solution for TCP perforating
Redress kits allow for quick turnarounds